As we all remember, during the pandemic the prices of oil dropped under $40-45/bbl. It was logical to assume that in such circumstances oil and gas companies wouldn’t have the resources to invest in innovations. However, the opposite occurred: industry leaders soon realized that remote technology was the only way to ensure business continuity and personnel safety during the crisis. Online operations and remote technical assurance allowed the industry to enter the new normal.
What the new normal of oil and gas companies is...
Remote technology turned out to be the ultimate solution to almost all challenges caused by the pandemic. First, it enabled monitoring field assets without violating the rules of social distancing. Second, it helped make businesses more cost-efficient and survive the turbulence. The statistics below confirm that remote monitoring has become one of the top priorities for organizations.
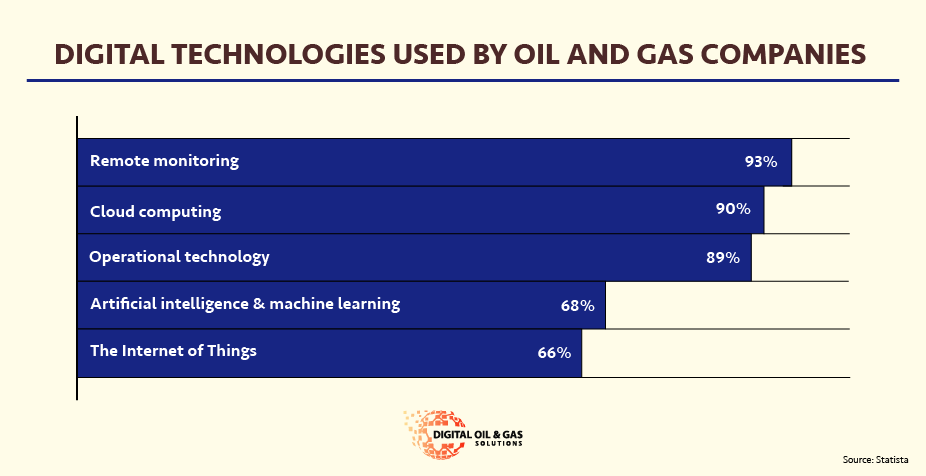
Thus, we see that technologies such as IIoT, wearables, and digital twin can strengthen an oil and gas company regardless of the company size and circumstances. Now, the industry doesn’t need a crisis to understand that remote technology is here to stay. Its value covers two aspects:
Improved people management and working conditions for employees
Improved awareness and decision-making for all involved in running the business
Here, we will examine both and explain why oil and gas companies will stick to remote technologies in the future.
How remote technologies improve operations for employees?
They bring the benefits of remote technical assurance
With COVID-19 travel restrictions, there was a risk that on-site teams would remain without expert support. But companies managed to turn these restrictions into a benefit by implementing remote survey solutions. With these technologies, distance doesn’t matter anymore. You can choose a specialist based on their expertise, not on their location. Moreover, you don’t have to wait for weeks or months to schedule a survey and organize travel and accommodation. Instead, you can quickly connect once a specialist is available.
The main benefits of remote technical assurance are that remote survey can be faster and even more precise than a physical inspection thanks to live-feed technology. During this procedure, on-site employees use their tablets to share high-quality videos and visuals with a surveyor. All the footage is documented, which gives the opportunity to re-access it for more detailed data if needed in the future.
They ensure higher employee safety
Since oil and gas companies started leveraging technology for remote inspections and maintenance-related activities, regular physical visits to locations were no longer required. This step was an absolute necessity during the COVID pandemic as it reduced the risk of spreading the virus.
Apart from mitigating this risk, such an approach solved one of the oldest and most painful problems of the industry: how to ensure the safety of the employees who work in a dangerous environment. The solution was rather unexpected: instead of trying to make this environment less dangerous, it turned out it was possible to physically take people out of the equation. Today, employees can complete remote inspections and conduct remote technical assurance without putting themselves at risk.
They build employee engagement
With operations moving online, it became vital to ensure the workforce adapts to digital reality to keep up its productivity. Remote technology came to the rescue again as it provided new ways of engaging employees. Today, team members can have more structured interactions instead of ad-hoc conversations. In such a scenario, people can communicate with those whom they were not likely to meet before. This leads to better knowledge exchange and helps build stronger teams.
A Deloitte report mentions that 59% of executives consider productivity and engagement of employees the biggest challenges of remote work. Therefore, it’s advisable to organize regular meetings with diverse agendas: from operational to entertaining. Such meetings give an excellent chance to educate your personnel leading to better productivity.
What value does the board get out of remote technologies?
Apart from the operational improvements described above, remote technology provides new opportunities for ambitious leaders to bring more business value. As stated by McKinsey, executives will need the following qualities to navigate their companies towards the new normal.

“Reform” and “Reimagination” presuppose sticking to new workflows powered by technology. It is the ultimate way to reach the following:
Improved remote decision-making
Any oil and gas company that has implemented IoT and data capture technology never have to fear travel restrictions again. Thanks to these solutions, data from field assets is broadcast to the board room without time delays. There’s no longer a need to wait for field workers to manually fill in all the papers and pass this data to management. Connected sensors and intelligent apps can do it instead of people: they provide all well, tank, and meter metrics on one easy-to-use interface. All this data is instantly available for review.
Moreover, such apps automatically calculate production, provide historical asset data and EHS and Greenhouse requirements. Having all this data easily available, oil and gas executives can make effective decisions from anywhere. All issues can be efficiently resolved, which results in higher business sustainability.
Ensured cost-efficiency
Implementation of a proper tech solution within an oil and gas company significantly reduces costs. First, it empowers boards to switch to a proactive business model and focus on preventing negative scenarios rather than dealing with them. Being Proactive and not Reactive. This starts with predictive maintenance and expands to technical assurance and cyber resilience.
As for the former, the use of smart sensors allows detecting any equipment malfunctions before emergencies occur, reduces downtime, and removes the need to spend money on damage coverage. In addition, remote technology helps find the perfect balance between asset performance and maintenance cost so that no investments in operations go in vain.
Implementation of better data security control
The opportunity to enhance your security is the other benefit presented by remote technology. While working offline, employees perform various tasks, from maintenance to technical assurance. Their interactions with multiple assets, including both OT and IT, are not always fully documented. Meanwhile, working online requires personnel to use corporate devices and log in daily to the system using their credentials. This provides the ability to manage data access and track all suspicious activities.
Why remote technologies are the future of the oil and gas industry
To sum up, let’s briefly review the benefits brought by remote technology that have secured its place in the industry’s future:
Improved working conditions and safety for field workers
Higher employee engagement
Streamlined knowledge exchange and technical assurance
Predictive maintenance and lower operational costs
Instant access to data from field assets
Improved data protection and security
Timely implementation of remote technologies in your business model is half the battle. However, it’s important to choose trustworthy technical partners with proven experience in the industry. Our team of professionals are ready to discuss how your business can benefit from remote solutions and meet the new normal fully armed.